今回はFA電気設計における実際の設計手順を解説します。機械設計仕様に基づき、まずは部品選定から電気回路設計までの手順を把握しましょう。
機械設計仕様の確認
最初に行うのは機械設計仕様の確認です。FA電気設計では機械の動作や性能要件に従って、どのような制御システムを構築するかを決定します。例えば、以下のような項目を確認します。
- 動作タイムチャート
機械設計者が作成した動作タイムチャートを確認しながら設計意図を理解します。タイムチャートの有無に拘らず、機械設計担当者の設計意図を理解するまで打ち合わせが必要です。 - 制御するモーターやシリンダーの仕様
コンベアで搬送する為のモーターの数や位置精度、電気仕様の確認、エアシリンダーを使用する場合は停止時の状態(その場停止やサイクル停止)や使用する電磁弁の電気仕様と数量を確認します。 - センサーの機能と位置
センサー設置用途や検出タイプ、配置箇所及び数量を確認します。 - 安全装置の有無やその仕様
非常停止の配置やセーフティライトカーテンの有無を確認します。
この段階で機械の各動作に対して必要な信号の種類や入出力点数を確定し、制御する範囲を明確にします。
部品選定①
次に電気設計で使用する部品を選定します。PLCの入出力点数や負荷容量に関わる以下の部品選定を行います。
- スイッチ
起動用の押しボタンスイッチや機種選択用のセレクタスイッチなど、操作目的を考慮して選定します。許容電圧/電流は勿論、微小な電流を流す場合には微小負荷仕様を指定します。 - センサー
検出対象(ワーク有無、圧力低下、シリンダ位置など)や設置条件に合ったセンサーを選定します。タイプは基本的にNPN出力を指定します。(シリンダに付属する位置センサは有接点出力タイプを使用することがが多いです) - ランプ
シグナルタワー(3~4色で点灯する積層ランプで、遠くからでも運転状態が把握出来るように高い位置に設置されます。)や表示ランプ等、用途に合った色や電圧仕様で選定します。スイッチと一体化した「照光スイッチ」を選定することも考慮します。 - 安全装置
非常停止スイッチ、セーフティライトカーテンなど、安全規格に準拠したものを選定します。 - PLC
処理速度や入出力点数、アナログ信号の読み書きや上位機器との通信要否を考慮して選定します。出力仕様は私の知る限り、一般的にトランジスタ出力のシンクタイプ(NPN)を指定します。 - タッチパネル
タッチパネルを搭載する場合は何の目的で使用するのか、画面サイズやグラフィック、電源仕様や使用するPLCとの通信方法も含めて選定します。PLCとメーカーが異なっていても通信は可能です。 - モーターやサーボモーター
機械設計者の設計意図より速度制御が必要であればインバータやスピードコントローラの選定、位置制御が必要であればステッピングモーターやサーボモーター、モータードライバを選定します。 - 電磁弁
エアシリンダを駆動する装置の場合、電磁弁はシングルソレノイド、ダブルソレノイドの選定をします。シングルソレノイドの場合、PLCの出力がOFFになったり電源がOFFになるとエアシリンダは必ず定位置に戻ります。ダブルソレノイドは切り替えた側の末端位置で保持される為、作業者の安全を考慮するとダブルソレノイドを選定することが多いです。ダブルソレノイドでもトラブル発生直後からその場でエアシリンダを停止させたい場合は3ポジションタイプを選定します。
選定には仕様、価格、納期も考慮します。メーカーや型番をリストアップし、最適な部品を選定することが重要です。
電力と電流値の計算
機器が正しく動作するためには各機器の消費電力を計算し、電源容量を決定します。電源設計で考慮するポイントは以下です。
- 機器の消費電力
装置で使用する全機器の定格消費電力を確認し、トータルでどのくらいの電力が必要かを計算します。AC負荷とDC負荷でそれぞれ算出します。 - 電圧と電流
AC/DCの電源電圧や使用する電流値を把握し、ケーブルや配線、この後選定するブレーカーの容量を決定します。
部品選定②
部品選定①と電力計算を経て、下記部品選定を行います。
- 電磁接触器、リレー
大きな電流をON/OFFするには電磁接触器、小さい電流をON/OFFするにはリレーが必要です。必要な仕様に合わせて選定します。 - スイッチング電源
主にDC24Vを使用します。PLCへの入力機器、PLCからの出力機器の電源として使用します。DC24V系の総負荷容量を算出し、余裕を持った容量を選定します。
※私は後の追加改造等も考慮して総負荷容量の1.5~2倍の電源を選定しています。 - 端子台
電源分配用であったり、外部機器との中継用として必ず必要になります。必要な個数、電流値などを考慮して選定します。 - ブレーカー
主電源供給用に設置します。極数(単相/三相)や電圧、電流、漏電検出有無を考慮して選定します。
※私は負荷電流の1.25倍以上の電流値を選定しています。
ここで選定した部品も含め、最終的な電力を算出します。
配線の選定
機器を正しく接続するための配線設計では、まず定格電圧、電流容量、電圧降下、耐熱温度、信号伝送の安定性を考慮します。特にFA電気設計では以下の点が重要です。
- パワーライン
モーターや大きな負荷を動かすラインには、適切な電線径(SQ / AWG)が必要です。過電流に耐えるために、余裕を持った配線径を選びます。電線の許容電流については以下のサイトを参考にしてみて下さい。私の取り扱う装置の設計上、制御盤内配線は「KIV」、制御盤外のケーブルは「300V VCTF」や「600V VCT」を使用します。これらを参考に、負荷電流は記載されている電流値の7割以下の電流値に収まるように選定しています。(あくまでも私の例ですので、実際に使用する電線で検討して下さい。)
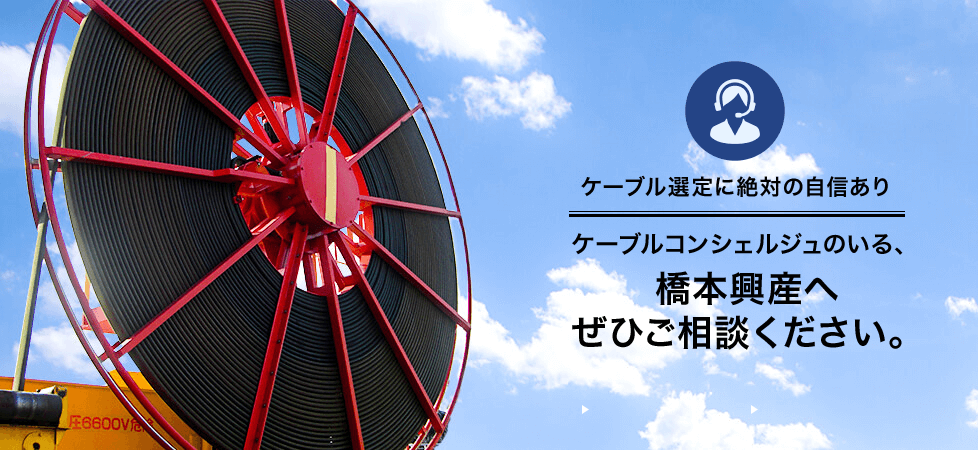
- 接地線
漏電検出や感電防止の為、工場内電源供給側の接地端子と装置側接地端子間に必ず接地線を接続します。電流容量によって適切な電線径を選定します。 - 信号線
センサーや通信線は微小電流の為、電流値よりもノイズ対策を考慮し、シールドケーブルやツイストペア線を使用することが推奨されます。特にPLCのアナログ入力信号は外部ノイズの影響を避けるために注意が必要です。 - 配線ルート
配線ルートの設計も重要で、電源ケーブルと信号ケーブルは分離し、交差する場合は直角にするなどの基本ルールを守ることでノイズ対策を行います。
電気回路図の作成
電気回路図はシステム全体の設計図となり、設置や配線、メンテナンスにも使用されます。以下の内容を盛り込みながら電気回路図を作成します。
- 主回路図
電源から機器への電力供給ルートを示します。 - 制御回路図
スイッチやセンサー、PLCの入出力を表します。 - 安全回路図
非常停止スイッチやセーフティリレーなどの安全装置を明示しますが、私個人としては主回路図で明示することが殆どです。
NPNオープンコレクタ仕様のセンサ接続について
PLC周辺の接続方法は基本的にPLCの記事でも説明している通りですが、工場の生産ラインで使用されるセンサはNPNオープンコレクタ仕様のものが多いです。こちらの接続方法も説明します。
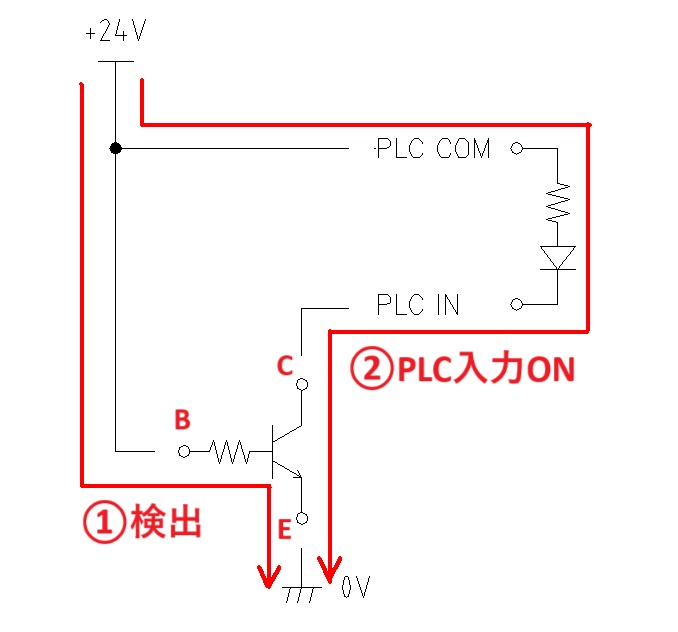
NPNオープンコレクタ仕様のセンサは検出すると①の方向でB-E間に電流が流れ、C-E間がONになります。コレクタ端子が出力となってPLCの入力アドレスに接続されている為②の流れで入力アドレスがONします。
接続方法は一般的に茶色線を+24Vに接続、青色線を0Vに接続し、黒(白の場合もあります)色線をPLCの入力アドレス端子に接続します。
電気回路の作成方法について
通常はCADソフト(AutoCADなど)を使って、正確で読みやすい回路図を作成します。まずは操作に慣れることを優先し、下記のような単純な回路から徐々にステップアップして設計するという手法が良いと思います。
下記回路がどのような動作をするか、少し考えてみて下さい。
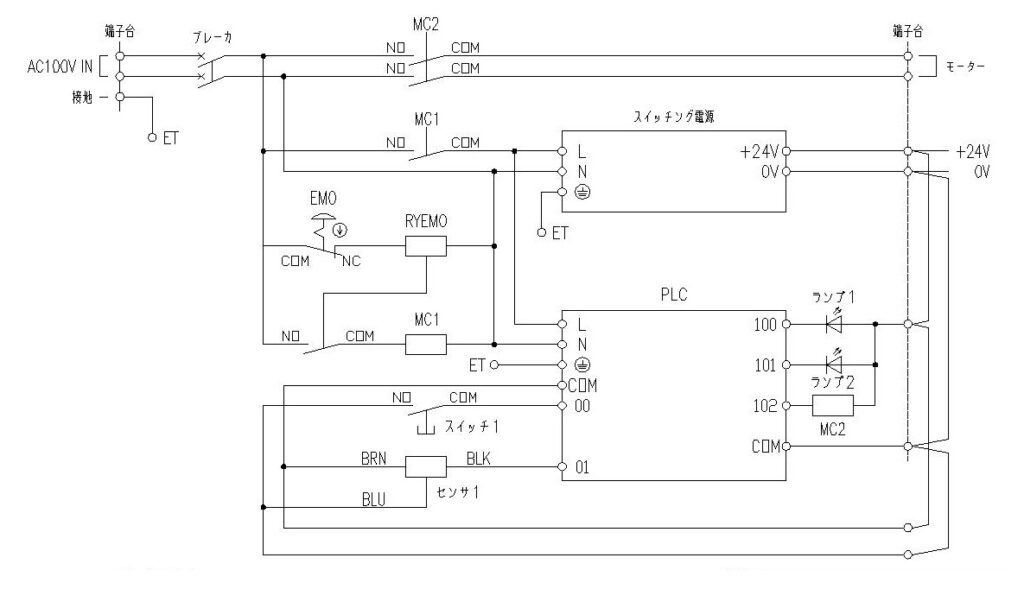
それでは回路について説明します。
端子台に供給電源(この場合はAC100V)を接続し、ブレーカーをONした状態から考えます。
- 非常停止スイッチ(EMO)が押されていない状態であればRYEMOがONし、MC1がONします。
- MC1がONすると、スイッチング電源とPLCに電源が供給され、スイッチング電源からDC24Vが出力されます。
- スイッチ1をONするとPLCの入力000がON、センサ1がONすると入力001がONします。
- PLCのプログラムにより出力100がONするとランプ1が点灯、出力101がONするとランプ2が点灯します。
- 出力102がONするとMC2がONになり、モーターへ接続される端子にAC100Vが供給されます。
- 非常停止スイッチを押すとRYEMOとMC1がOFFになり、スイッチング電源とPLCへのAC100Vが遮断されますので、結果的にブレーカーより後方の全機器が動作不能になります。
理解の程は如何ですか?
まとめ
電気設計について初期の仕様検討から正確な部品選定や配線設計までを解説しました。
電気回路設計が完了したら、いよいよラダープログラムの設計です!
ラダープログラム設計については下記の記事が参考になれば幸いです。それでは!
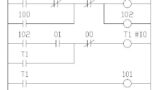